What is a machine vision system?
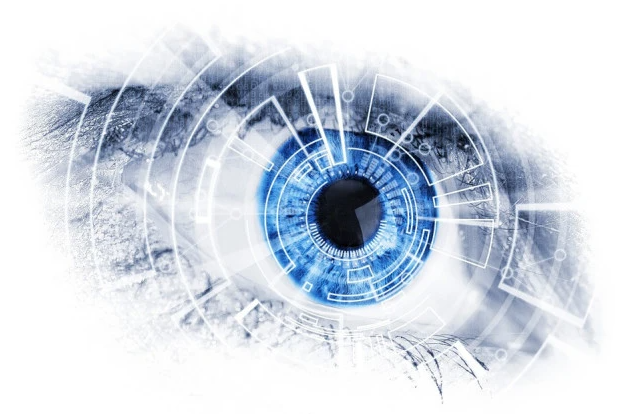
The application of machine vision in automatic measurement system is more and more popular. The reason is that more and more information needs to be extracted from the camera, rather than from special sensors. The camera can be used to extract temperature information, measure dimensions and check for the presence of objects and also provides many other useful information. This makes it widely used in quality testing, in machine control and robot guidance applications, all of which have unique needs and challenges when choosing control hardware and software.
1. What is machine vision system?
Machine vision system mainly studies the use of computers to simulate human vision functions, obtain images through the camera, then convert them into digital image signals, and then send them to the computer, use software to obtain the required information, correctly calculate and judge digital image processing algorithms and recognition algorithms, and control the equipment action on the scene according to the recognition results. Recognize three-dimensional scenes and objects in the objective world. In terms of function, a typical machine vision system can be divided into image acquisition part, image processing part and motion control part, and computer vision is an artificial intelligence recognition system that studies and tries to obtain the "required information" from images or multidimensional data. Widely used in medicine, military, industry, agriculture and many other fields.
2. Processing capacity
The powerful processing power can directly affect the operation algorithm and decision speed of the vision system. The processing power required by a single camera barcode detection system is significantly lower than that of a multi-camera 3D vision system. I/O or machine vision systems, such as closed-loop motion control, require higher processing power to ensure that the vision components and I/O motion control components can operate stably. To reduce image processing time, some manufacturers now use isomorphic processing to run vision algorithms. Using a combination of a CPU and a GPU, FPGA or DSP to process an image is much faster than using one of these components alone. Isomorphic processing can reduce the time required for image processing and even allow images to be used as inputs for closed-loop control algorithms. It is important to fully understand the algorithm and time required for the system before choosing the controller required for the vision system.
3. Camera support
The number of cameras used in image acquisition and the type of communication bus also affect the choice of controller. After selecting the camera required for your application, make sure that the controller can support using the camera's communication bus. The two industry standard buses commonly used in machine vision applications are USB3Vision and GigEVision. These standards allow controllers to connect to cameras using standard USB3.0 or Ethernet ports, which are common in consumer and industrial computers. Both standards allow multiple cameras to be connected to a single port via a hub or switch. This is a viable way to add more cameras to your system, but keep in mind that each camera connected to the hub shares bandwidth with the other cameras in the hub. In addition, most consumer-grade switches do not support Power over Ethernet (PoE) wait specific features. If you plan to use these features, or if your system does not have enough bandwidth to share multiple cameras, you may want to choose a controller with multiple independent control ports so that each camera gets the full bandwidth.
4. I/O function
Most machine vision systems require some basic digital I/O trigger camera or read encoder. For example, the vision system uses a camera mounted above the conveyor belt to detect the delivery parts. The difficulty is how to take an image while moving the camera directly under the part, unless the system can track the location of the conveyor belt. A common way to solve this problem is to use an encoder to read the location of the conveyor belt and trigger the camera by placing the time interval between the part and the conveyor belt. If the parts on the conveyor belt are not evenly spaced, a trigger camera close to the sensor can be used.
Some machine vision systems may require more advanced I/O functions. In some applications of material analysis, it is often necessary to synchronize the image with the measurement data so that events in the image can be associated with the measurement data. Imagine an application that uses a camera and strain gauge to measure the curvature and load of a composite material when external forces are applied. These synchronized data can be used to understand how a material behaves under external forces, and even to measure the breaking point of a material.
This level of synchronization requires that image acquisition and I/O can be tightly integrated so that measurement data can accurately mark time, or that the camera and measuring device can share the same clock. Before choosing a controller, you need to know your controller I/O and synchronization needs. For basic measurements, such as triggered or asynchronous measurements, I/O requirements, you can choose an integrated or network distributed I/O controller. For more complex I/O needs, you can choose to integrate I/O or connect an I/O device controller via EtherCAT deterministic communication protocol.
Die Produkte, an denen Sie interessiert sein könnten
![]() |
3845 | 3X4 MATRIX KEYPAD | 7542 More on Order |
![]() |
3426 | RUGGED METAL ON/OFF SWITCH | 2178 More on Order |
![]() |
1188 | SWITCH PUSHBUTTON SPST-NO GRN | 563 More on Order |
![]() |
1194 | SWITCH PUSHBUTTON SPST-NO BLUE | 8334 More on Order |
![]() |
1187 | SWITCH PUSHBUTTON SPST-NO WHT | 8802 More on Order |
![]() |
2831 | SENSOR PHOTO TOP VIEW RADIAL | 5004 More on Order |
![]() |
981 | MAXSONAR RANGEFINDER LV-EZ3 | 6624 More on Order |
![]() |
3397 | OPTOMAX DIGITAL LIQUID LEVEL SEN | 6324 More on Order |
![]() |
658 | AC/DC DESKTOP ADAPTER 5V 50W | 9108 More on Order |
![]() |
584 | WIRE STARTER PK EL GRN 2.5M-8.2' | 8496 More on Order |
![]() |
586 | WIRE STARTER PK EL ORN 2.5M-8.2' | 7380 More on Order |
![]() |
406 | ELECTROLUMINESCENT WIRE YLW 2.5M | 8640 More on Order |
![]() |
2038 | ADDRESS LED MATRIX I2C WHITE | 5022 More on Order |
![]() |
3729 | ADDRESS LED MODULE SERIAL RGB | 6174 More on Order |
![]() |
2508 | ADDRESS LED STRIP SERIAL RGB 1M | 6624 More on Order |
![]() |
2328 | ADDRESS LED STRIP SERIAL RGB | 7182 More on Order |
![]() |
2963 | ADDRESS LED STRIP SERIAL RGB 1M | 6174 More on Order |
![]() |
2968 | ADDRESS LED STRIP SERIAL RGB 1M | 5112 More on Order |
![]() |
880 | ADDRESS LED 7 SEG I2C GREEN | 7578 More on Order |
![]() |
2239 | ADDRESS LED STRIP SERIAL RGB 4M | 5544 More on Order |
![]() |
2969 | ADDRESS LED STRIP SERIAL RGB 1M | 8244 More on Order |
![]() |
4117 | FLEXIBLE SILICONE NEON-LIKE LED | 4986 More on Order |
![]() |
188 | GRAPHIC KS0108 LCD 128X64 + EXTR | 4392 More on Order |
![]() |
1770 | 2.8"" TFT LCD TOUCHSCREEN | 2100 More on Order |